RUBBER & TIRES
Keep your tire and rubber
mold presses running
Buildup of cured material and mold release agents causes sticking
molds, blemishes and unwanted flash on final parts, making
them unusable and requiring press shutdown for cleaning.
Traditional cleaning methods can be time consuming, ineffective,
damaging to molds and result in high labor and material costs.
Dry ice blasting is an in-place, online or offline, quick and
effective way to clean without damaging expensive molds.
CASE STUDIES
Revolutionize processes
to drive real results.
Rubber Mold Cleaning
Improve product quality while reducing production downtime
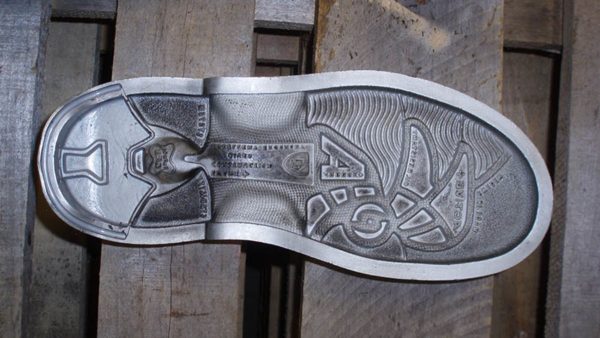
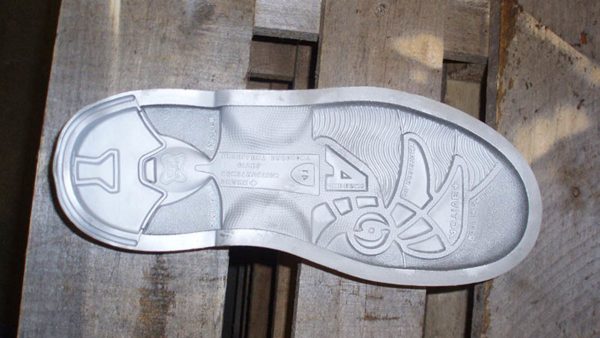

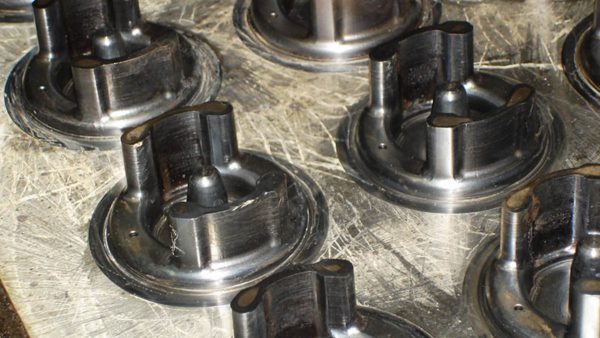
BENEFITS
Dry ice blasting safely cleans rubber molds while hot and online, reducing downtime and eliminating mold fouling.
- Eliminate complete shutdowns
- Clean in-place
No mold disassembly - Improve product quality and reduce scrap
- Non-abrasive
No impact damage or mold erosion - Increase production time
- Reduce cleaning time and labor costs
- Environmentally responsible
No secondary waste
SPECIFIC USE CASES:
- Injection molds
- Blow molds
- Compression molds
- Silicone rubber injection molds
- Metal bonded molds
- Lift presses
- Tilt back presses
Tire Mold Cleaning
Reduce production downtime by effectively cleaning tire molds online
BENEFITS
Dry ice cleaning extends running times and reduces defects and scrap rates by cleaning tire molds in-press without damaging spring vents.
- Reduce production downtime
- Decrease scrap rates and defects
- Non-abrasive
No impact damage - No tire mold disassembly
- Labor cost reduction of up to 75% when cleaning online
- No secondary waste
- Environmentally responsible
SPECIFIC USE CASES:
- Steel tire molds
- Aluminum tire molds
- Coated tire molds
- Segmented tire molds
- Two piece tire molds
- Spring vented tire molds
- Tire molds with complex surface patterns
- Lift presses
- Tilt back presses
BENEFITS OF DRY ICE BLASTING
Eliminate mold fouling and production
downtime by safely cleaning molds online
Dry ice blasting allows rubber and tire molders to clean their molds in-press, at operating temperatures. Cleaning molds online eliminates complete shutdowns, reduces production downtime and improves product quality.
→ Eliminate complete shutdowns and reduce downtime
→ Clean hot and online
No mold disassembly or cooldown required
→ Reduce scrap rates and eliminate reassembly damage
→ Non-abrasive
Will not damage or erode molds
→ Reduce cleaning time and labor costs
→ No secondary waste stream
→ Environmentally responsible
No secondary waste
→ Employee safe
Eliminates manual cleaning and exposure to unsafe conditions