FOOD & BEVERAGE
Experience a cleaner clean
with a fraction of the waste
Food processing and packaging equipment accumulates grease, carbonised
residue, seasonings, proteins, harmful bacteria, biofilms, adhesives, labels
and many other contaminants that traditionally take significant time to clean.
Dry ice cleaning provides an in-situ cleaning solution that is non-destructive,
sustainable, does not use water or chemicals and does not produce secondary waste.
CASE STUDIES
Revolutionize processes
to drive real results.
Processing & Packaging Equipment Cleaning
Increase line productivity by
getting a cleaner clean in less time
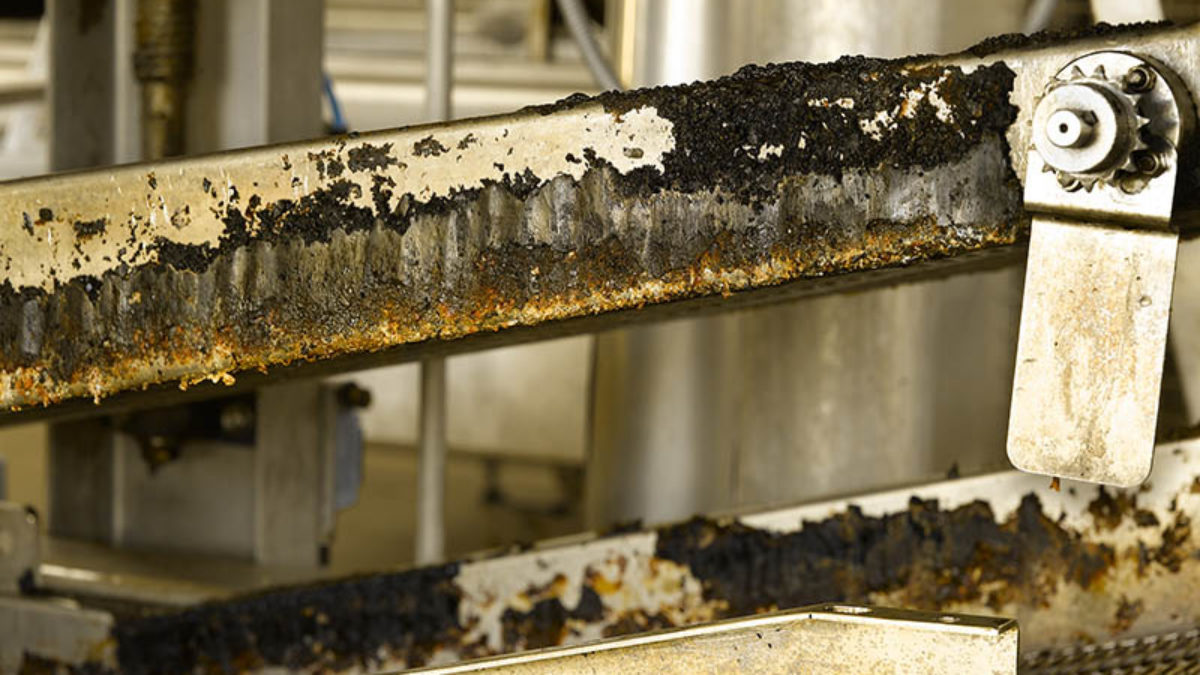
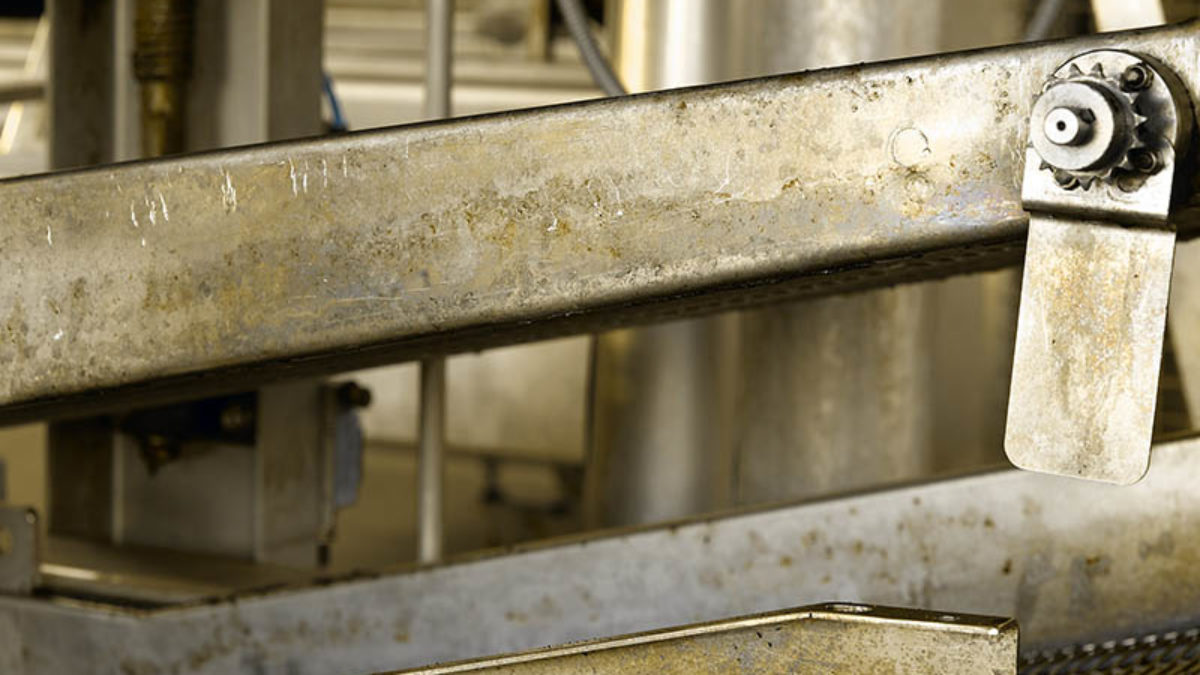
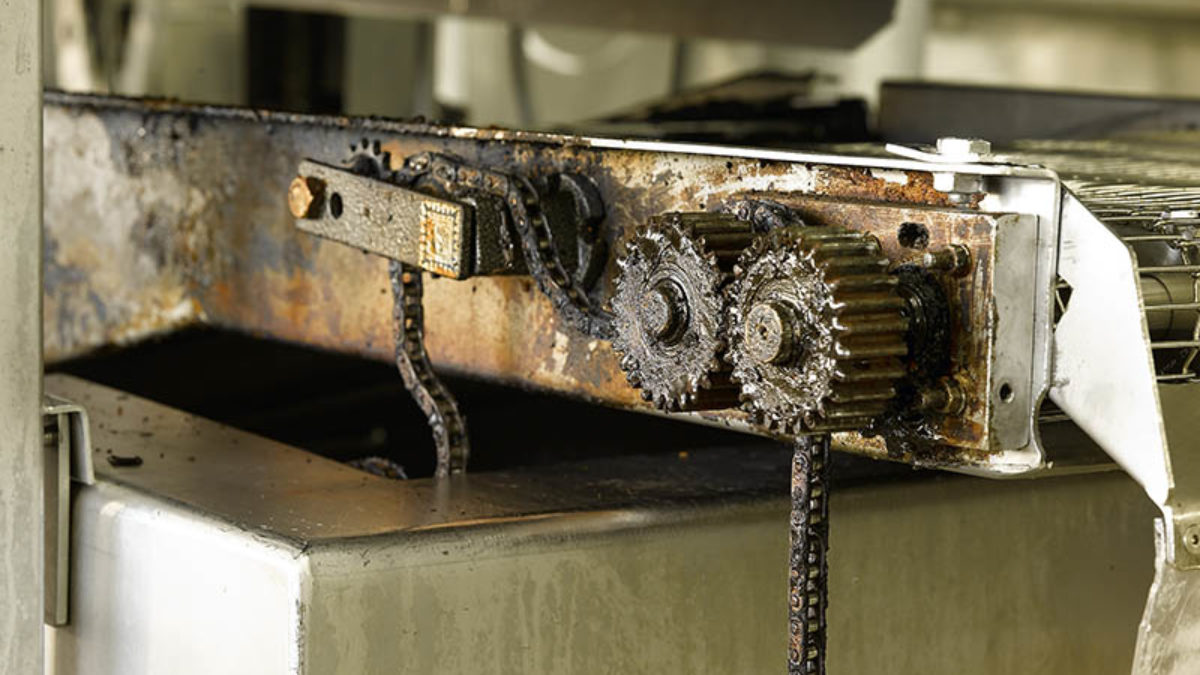
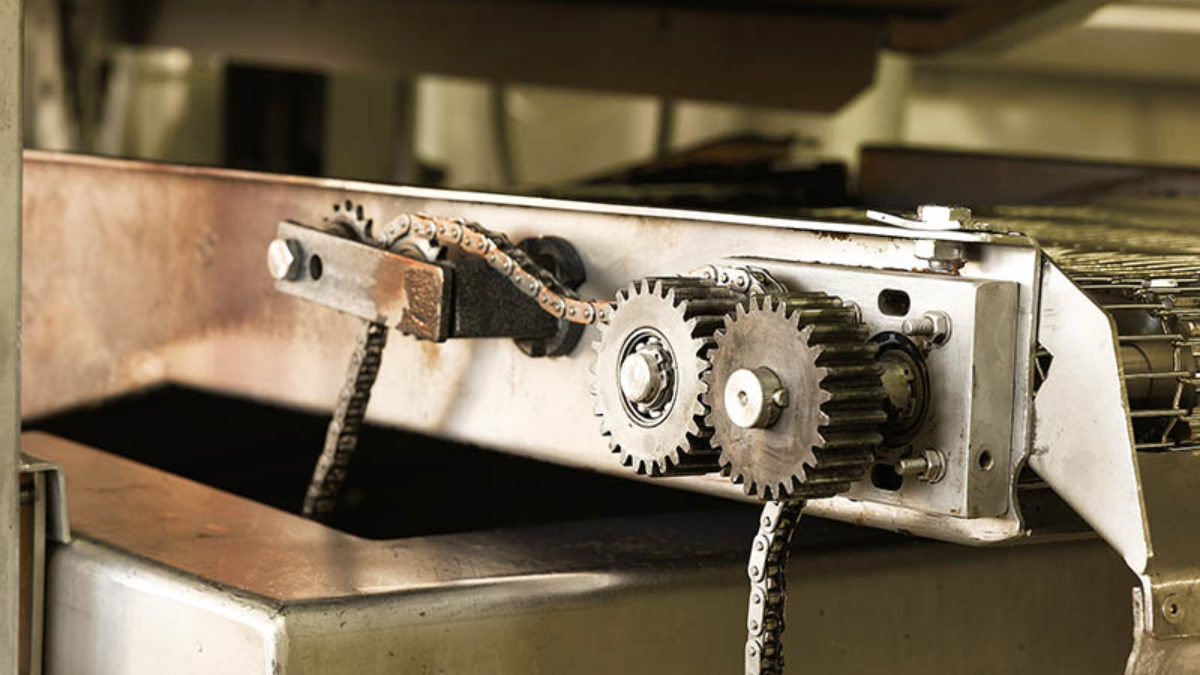
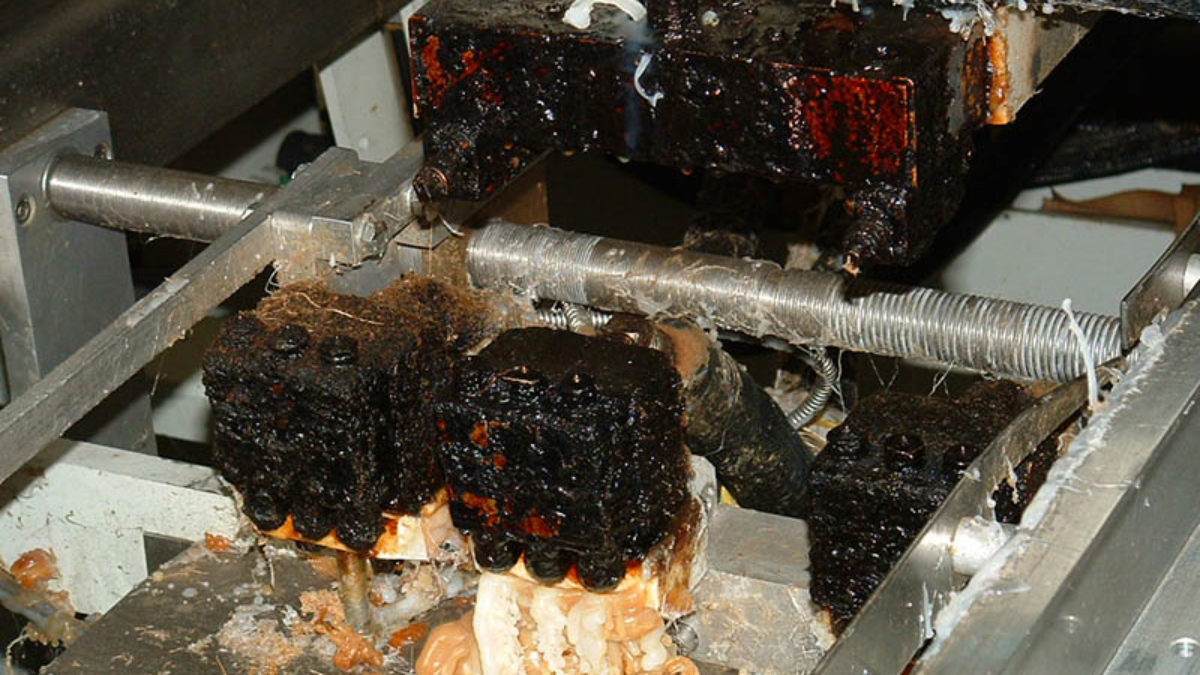
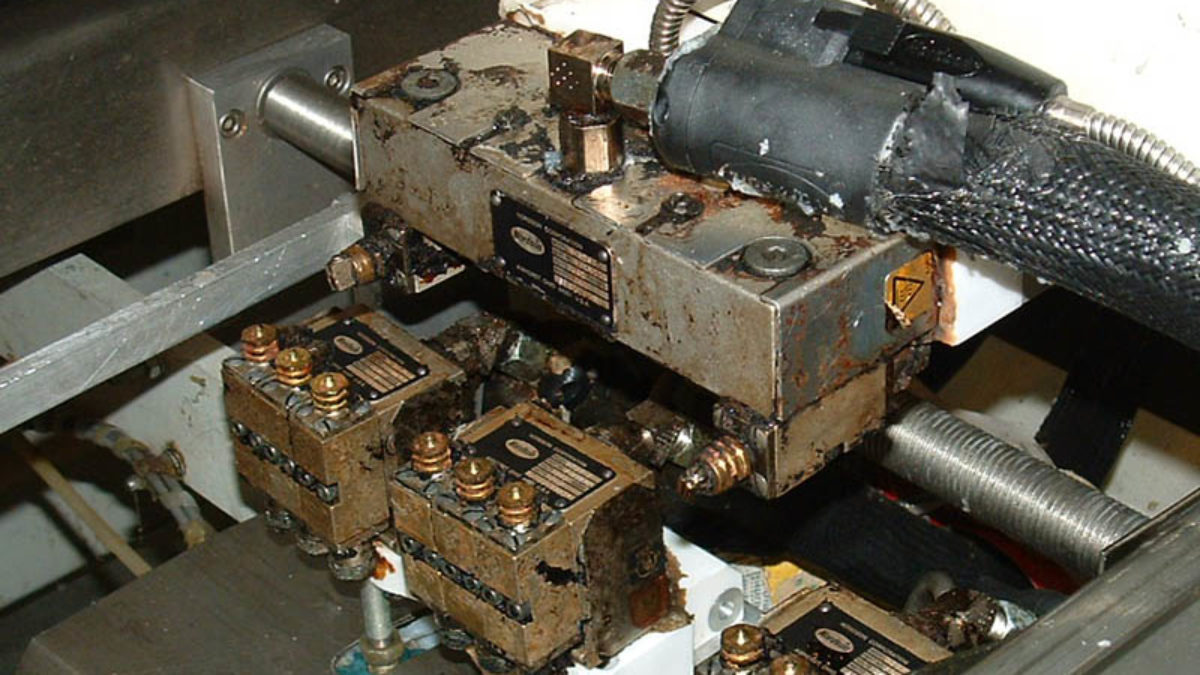
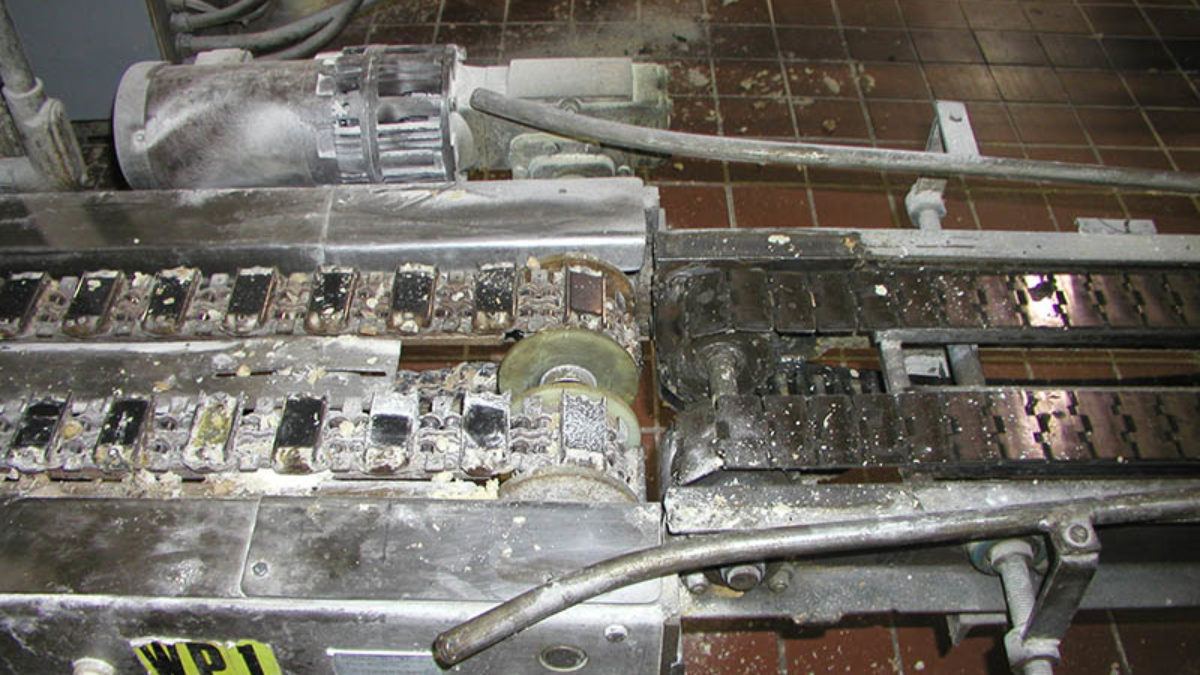
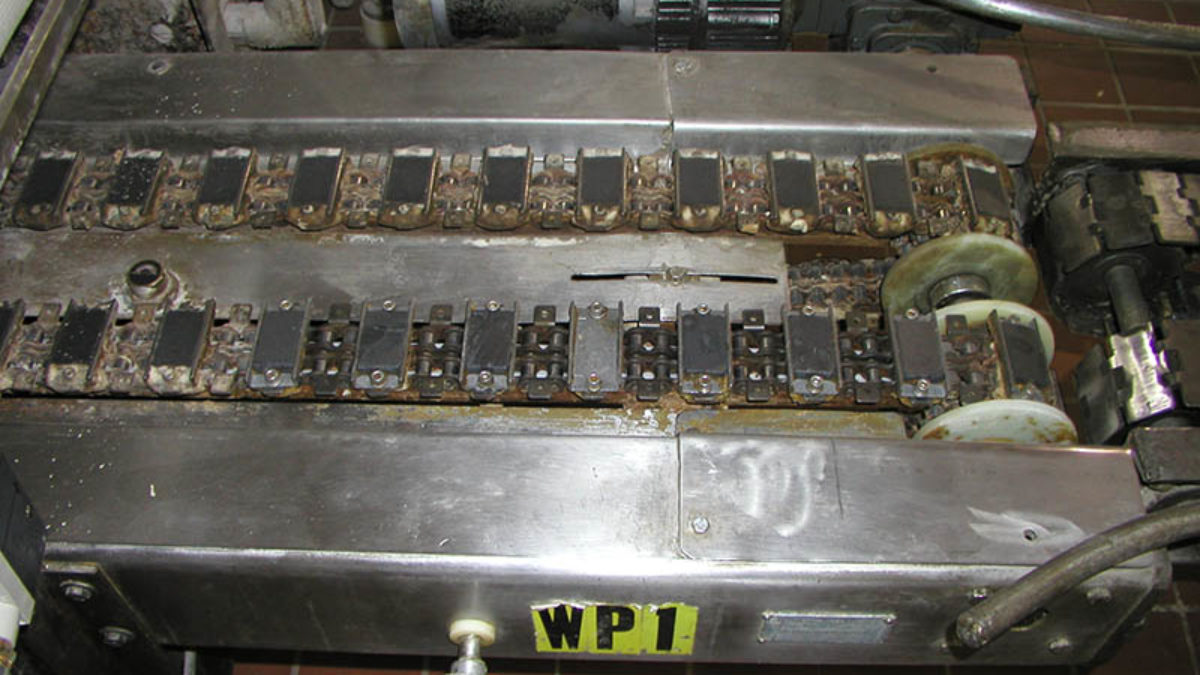
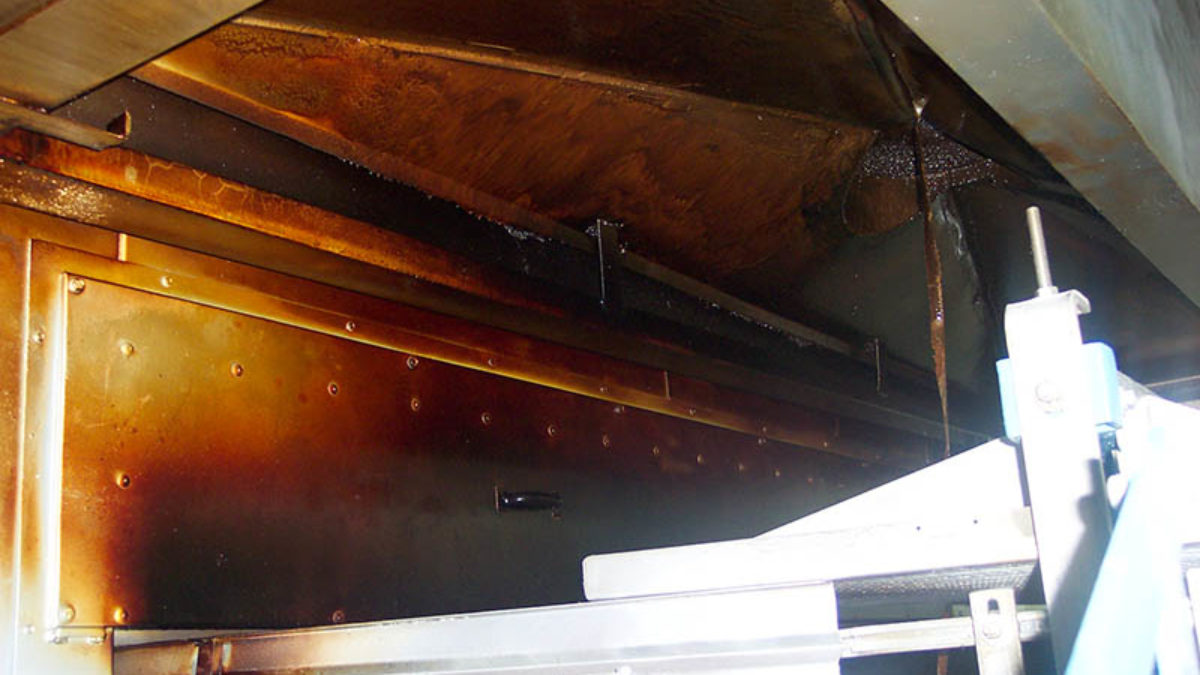
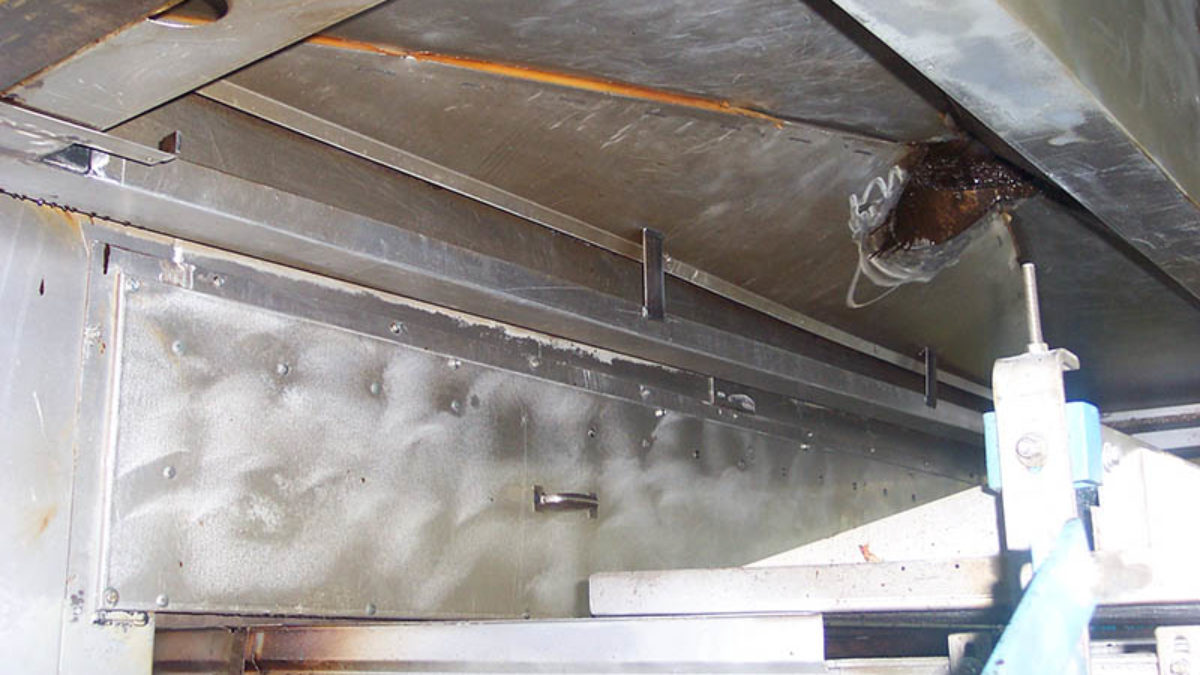
BENEFITS
Dry ice blasting thoroughly cleans contamination from process and production equipment in-place, without water or chemicals, and even while the equipment is still running.
- Reduce cleaning time and resulting downtime
- Clean hot and online
- No secondary waste
- Non-Abrasive
- Will not damage equipment
- Get a cleaner clean
- Reduce bacteria counts and remove biofilms
- Reduce risk of unplanned production stoppages and costly repairs
SPECIFIC USE CASES:
- Mixers and blenders
- Slicers and dividers
- Roasters, ovens and proofers
- Dryers, extruders and molds
- Conveyors and chains
- Radial feeders (Ishida Weighers)
- Wrappers and packagers
- Baggers and pack-off tables
- Labelers, box formers and glue applicators
- Mills and load-out bins
- Palletizers and de-nesters
- Electrical components and motors
- Cold storage
BENEFITS OF DRY ICE BLASTING
Dry ice blasting is a dry cleaning
process that does not produce
secondary waste or residue
Dry ice cleaning offers an effective, dry, sustainable and non-destructive cleaning method that can be performed in-place, which eliminates or reduces costly shutdown time for cleaning. Hard to reach corners and crevices are easily cleaned with dry ice blasting, resulting in an improved overall clean in your plant.
Not only does dry ice cleaning remove contaminants, but it will also result in log reductions in bacteria counts and will remove biofilms without water or chemicals* – all while significantly reducing cleaning time, labor and overall costs.
→ Clean online or in place, even while equipment is hot and running
→ Eliminate or drastically reduce disassembly
→ No water, chemicals or secondary waste streams
→ No masking or drying time
→ Non-conductive
Clean electronics, sensors and motors without damage
→ Reduce cleaning time and labor costs
→ Remove biofilms without water or chemicals
→ Lower bacteria counts (significant log reductions)*
→ Environmentally responsible