MEDICAL DEVICE
Maintain high product quality
by efficiently cleaning medical
device manufacturing equipment
Dry ice cleaning reduces cleaning time of precision molds
as well as precision and high-tolerance medical parts.
CASE STUDIES
Revolutionize processes
to drive real results.
Mold Cleaning
Improve productivity by reducing downtime
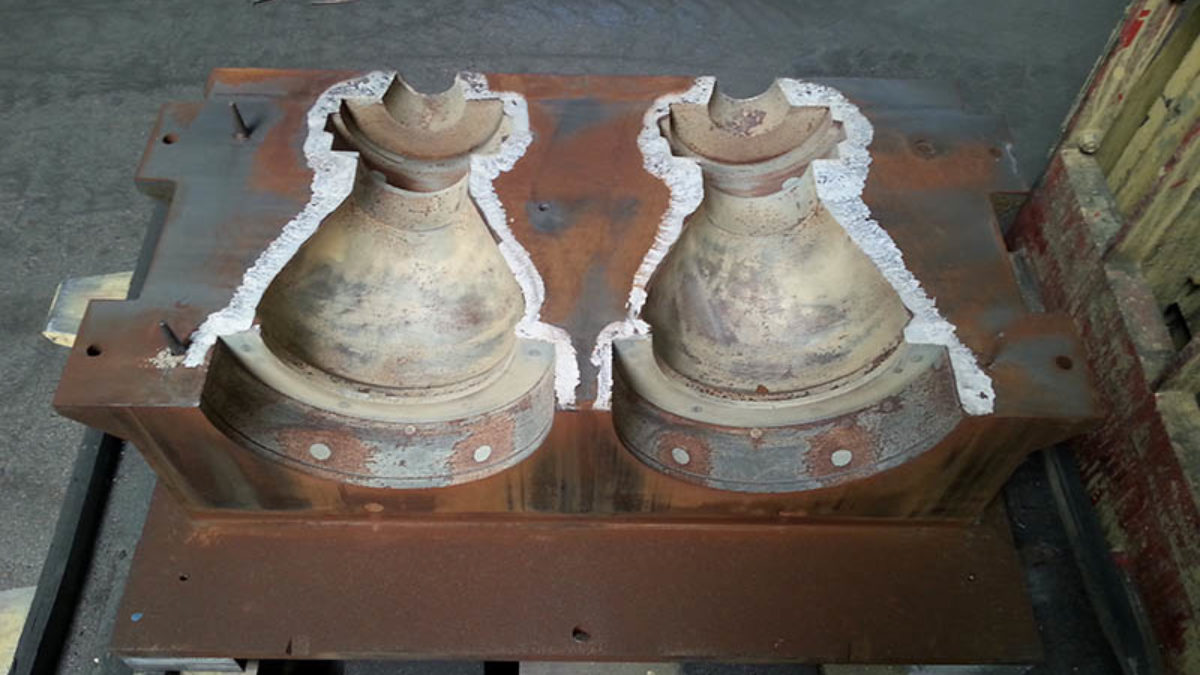
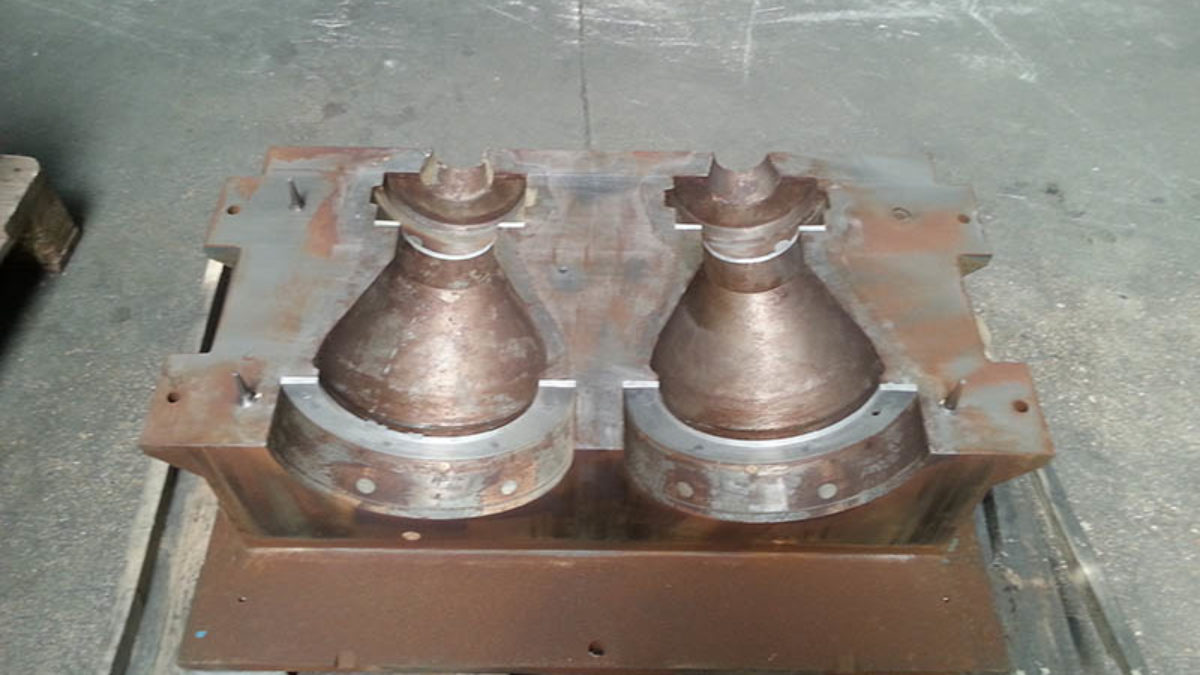
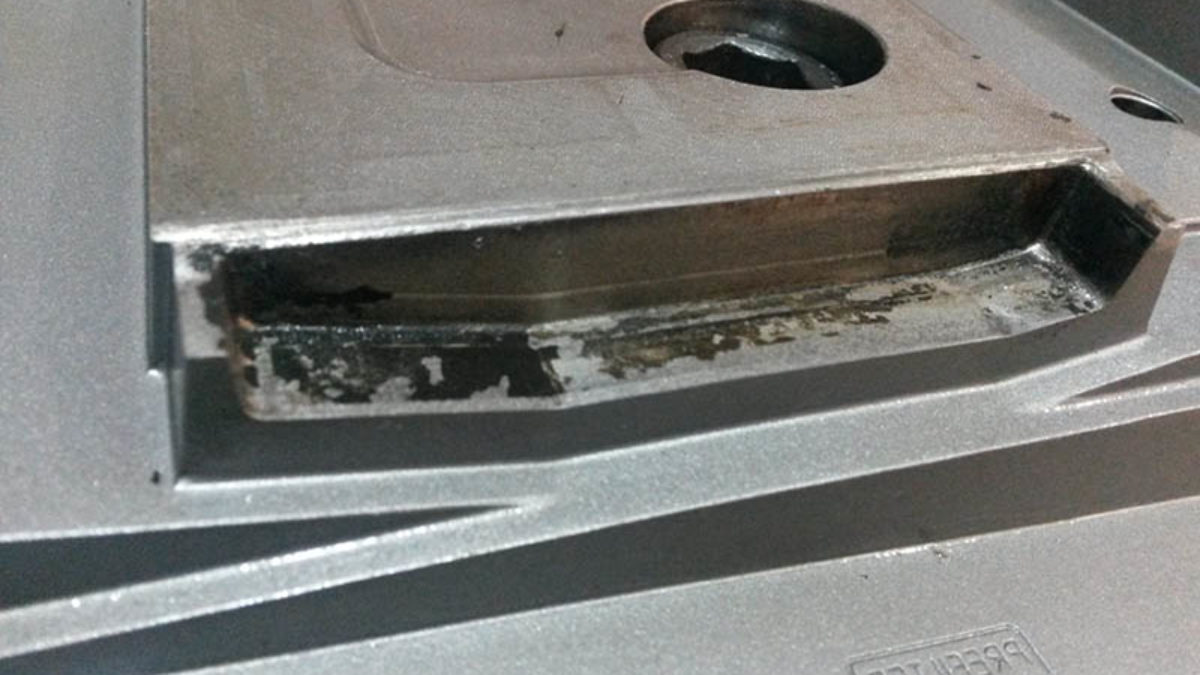
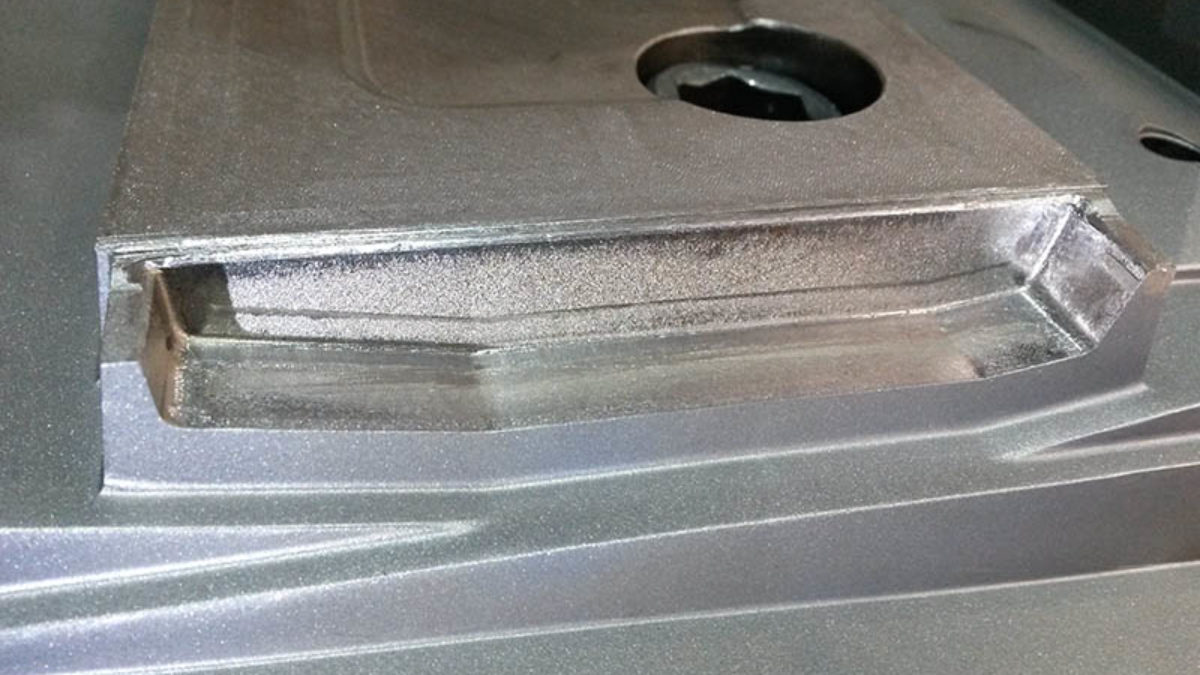
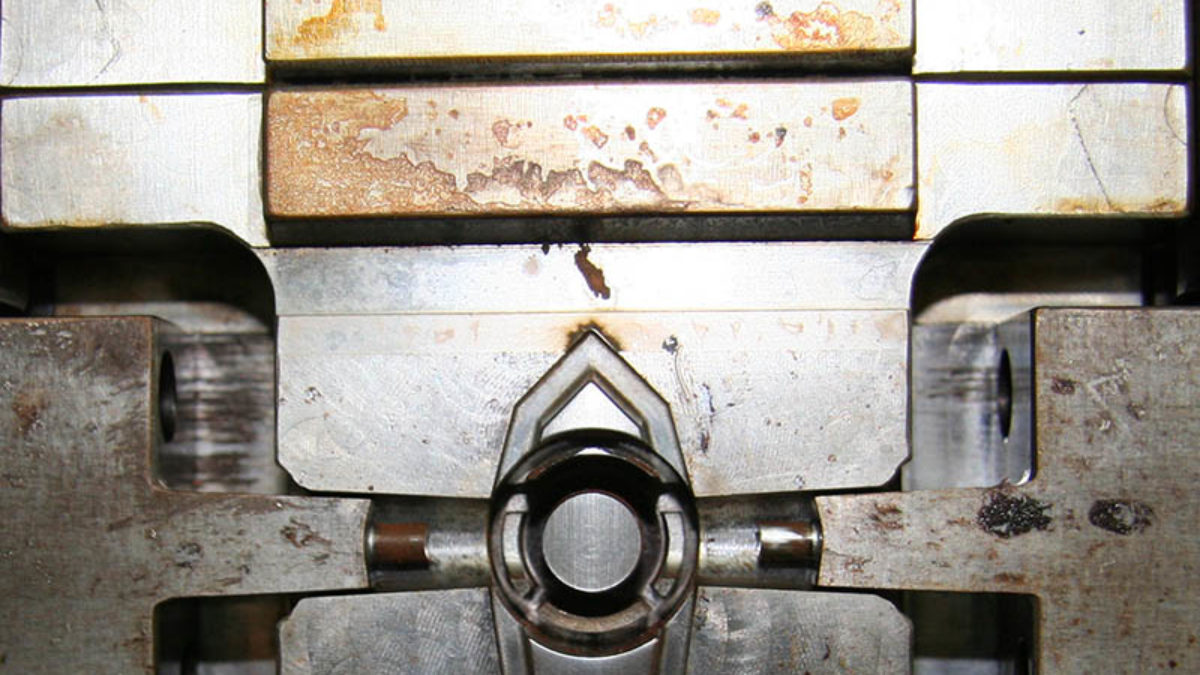
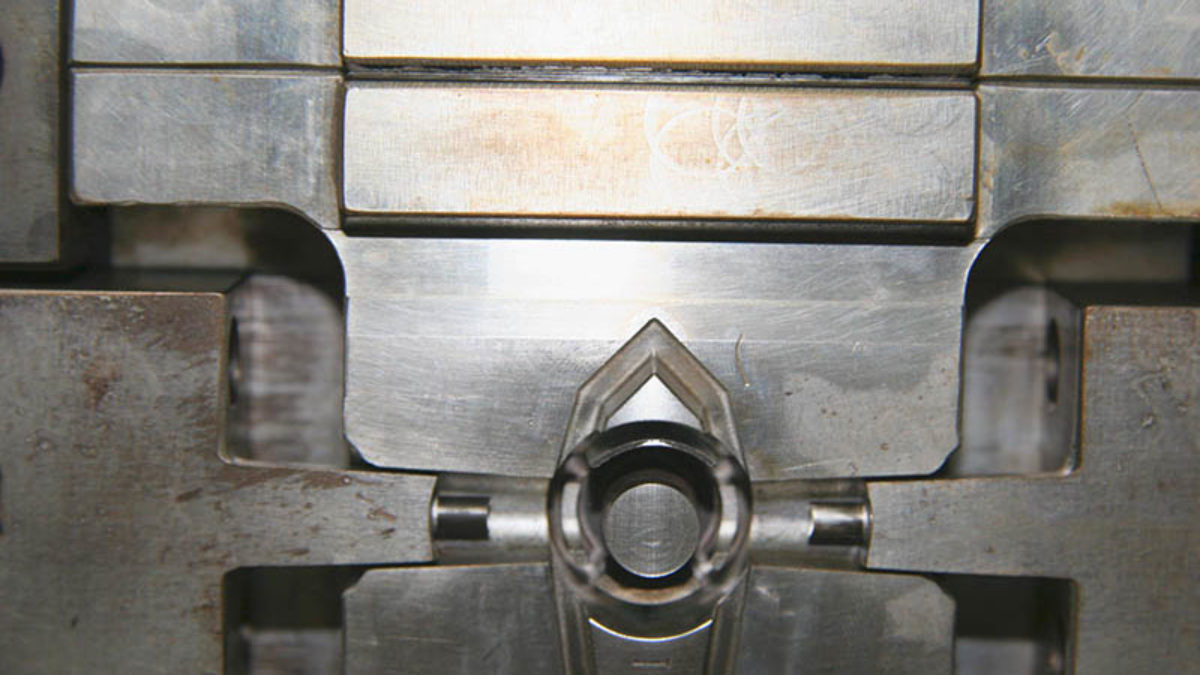
BENEFITS
Dry ice blasting is a non-abrasive method that safely cleans molds online, at operating temperatures.
- Improve product quality
- Clean in-place
Little to no disassembly required - Non-abrasive
No damage to molds - Reduce scrap
Cleaner molds lead to higher quality - Meet stringent industry demands
6-Sigma, Kaizen, 5S, TPM (Total Productive Maintenance) - Reduce production downtime
Clean quicker and without cooldown or disassembly - Decrease cleaning time and labor costs
- Eliminate painstaking manual cleaning
SPECIFIC USE CASES:
- Injection molds
- Blow molds
- Compression molds
- Urethane molds
- Textured molds
- Slush molds
- Technical molds
- Extrusion dies
- Rotational molds
- LSR and LIM molds
- Thermoform molds
Parts Finishing Cleaning
Quickly and safely deburr and deflash parts
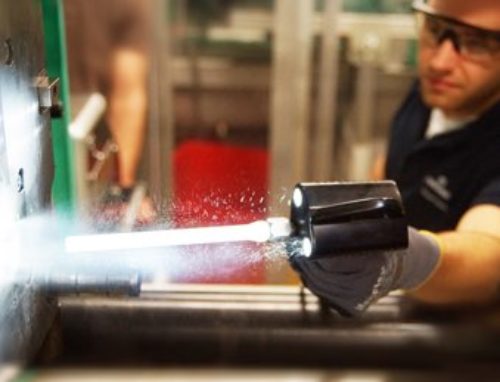
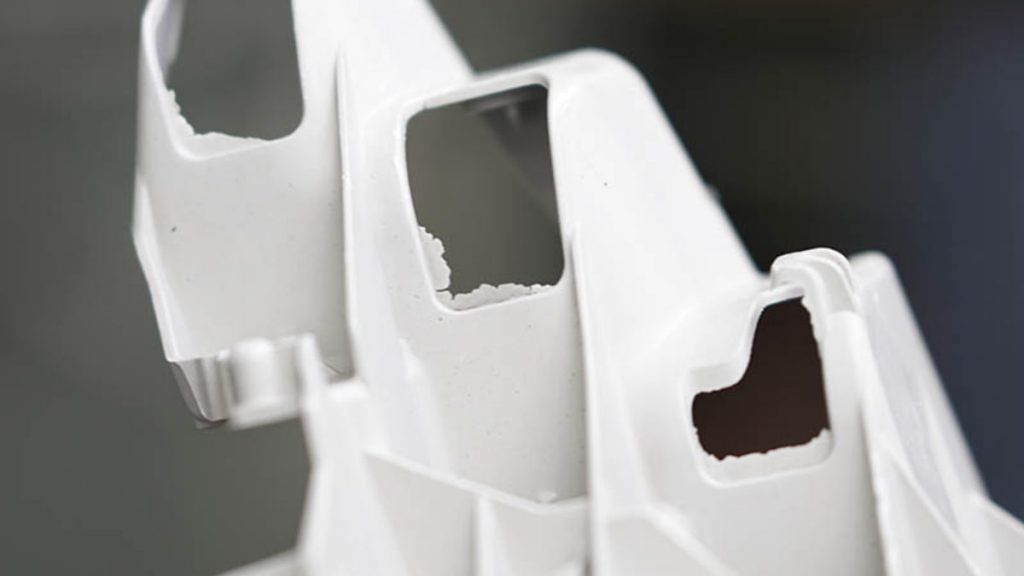
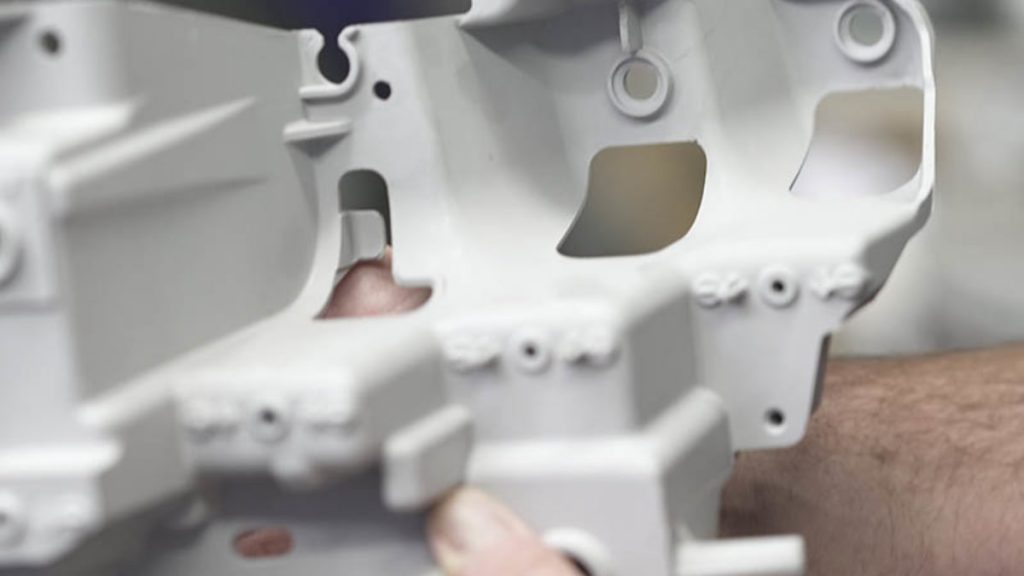
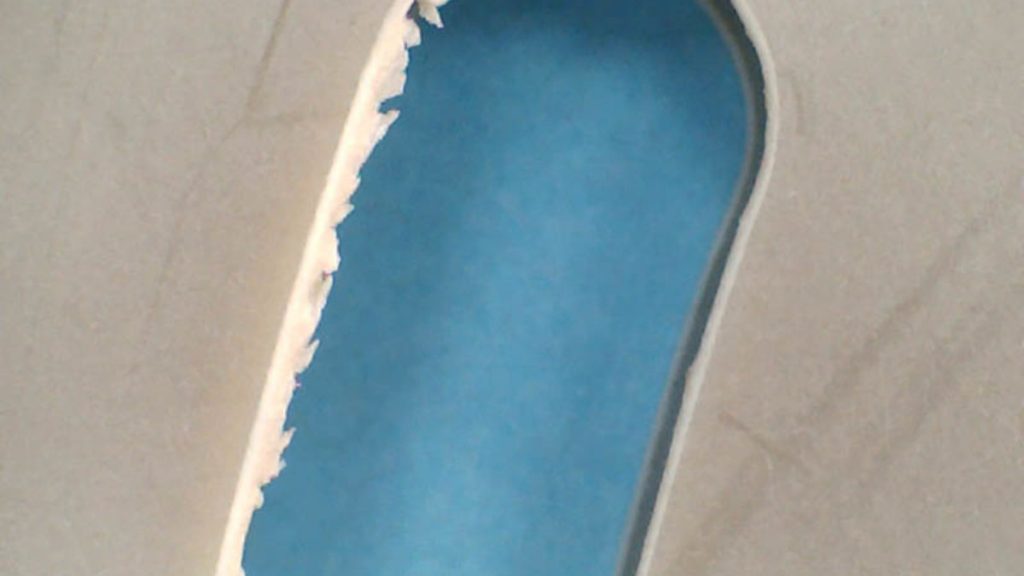
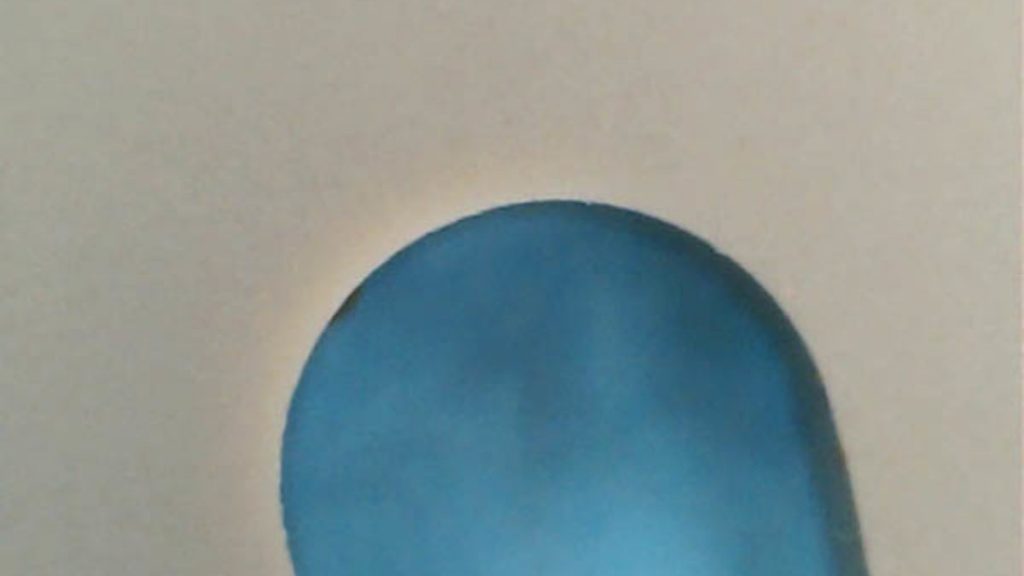
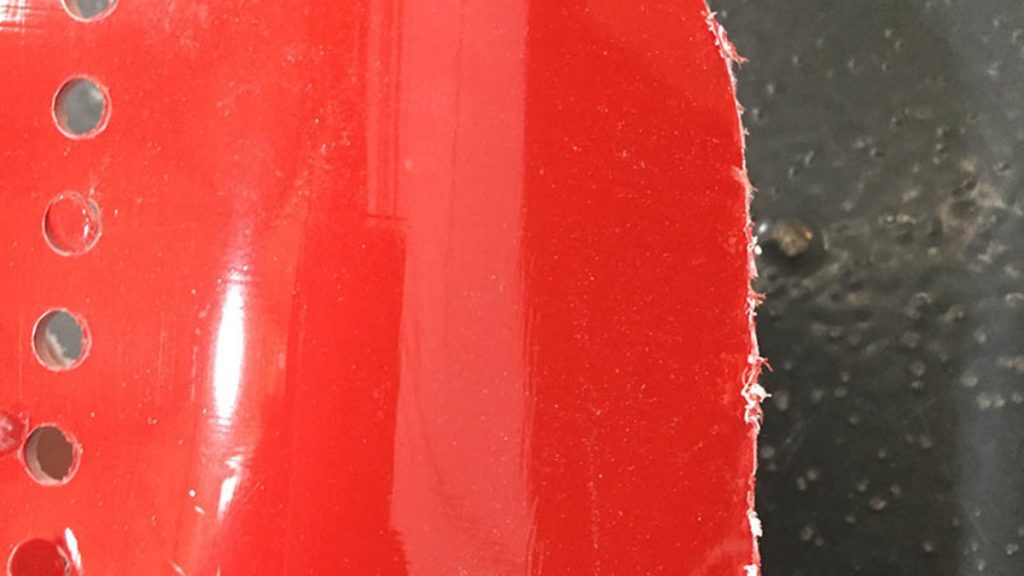
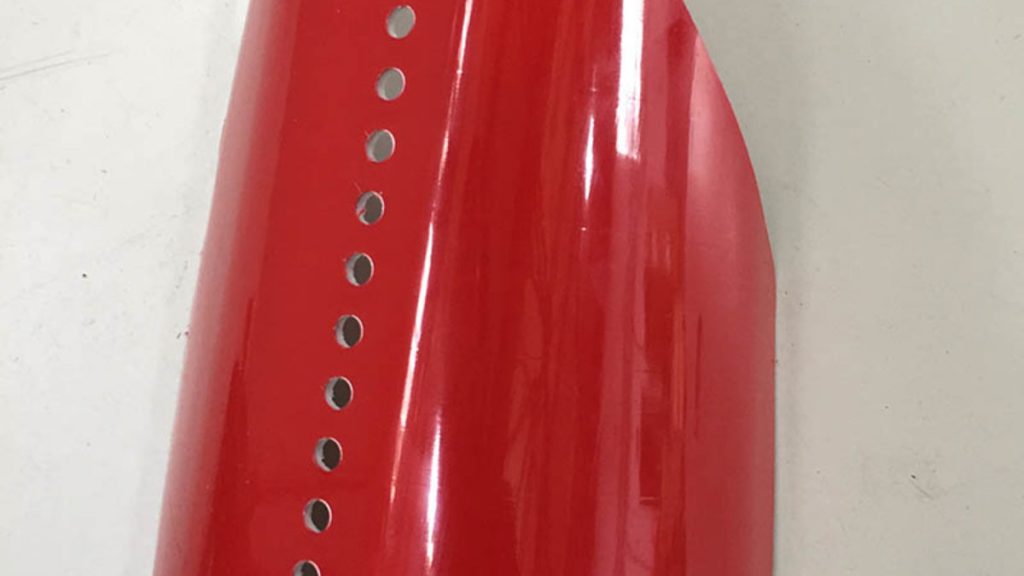
BENEFITS
Dry ice cleaning is a faster and more uniform flash and burr removal process that does not cause damage to the part.
- Faster and more uniform clean
- Elimination of cross contamination
- Non-abrasive
Lower scrap rates - Reduce cleaning costs and overall downtime
- Higher quality parts
- Eliminate manual cleaning
SPECIFIC USE CASES:
- PEEK
- PBT
- Acetal
- Nylon
- LCP
- ABS
- UHMWPE
- Nitinol
BENEFITS OF DRY ICE BLASTING
Meet stringent industry process
demands for quality and consistency
Dry ice cleaning safely and thoroughly cleans the complex cavities and vents of medical molds, as well as quickly removes burrs and flash from finished medical parts – enabling the consistent production of high quality products.
→ Decrease cleaning time and labor costs
→ Non-abrasive
No damage to product or equipment
→ Clean in-place
No disassembly required
→ Increase productivity and reduce downtime
→ Non-conductive cleaning process
→ Employee safe
Reduce harmful chemicals and tedious manual cleaning
→ Environmentally responsible
→ Improve part quality and reduce scrap
→ No secondary waste stream